å庫ã¬ã€ã¢ãŠããšã¯ïŒå¹æçãªèšèšææ³ãšã¬ã€ã¢ãŠãäŸ
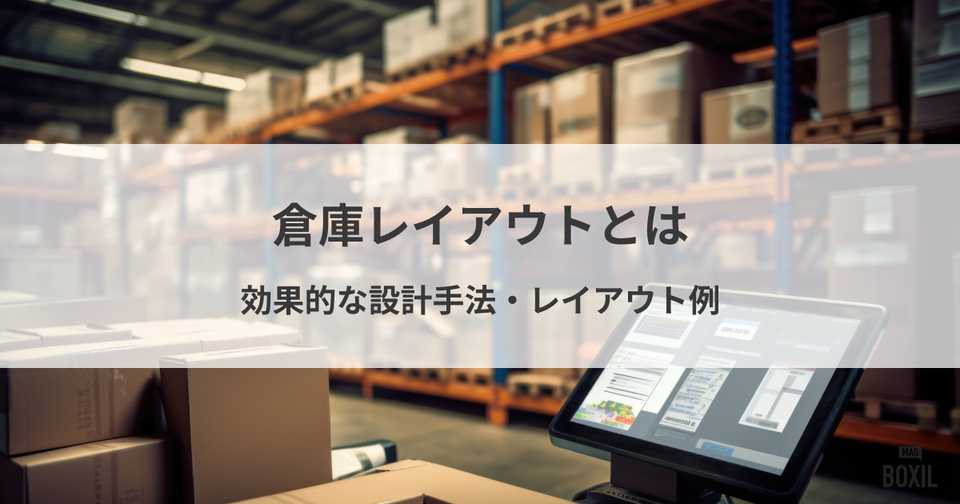
ç®æ¬¡ãéãã
- å庫ã¬ã€ã¢ãŠããšã¯
- å庫ã¬ã€ã¢ãŠããæé©åããã¡ãªãã
- ç©æµå¹çã®æé©åãšäœæ¥å¹çåäž
- äœæ¥æéã®ççž®ãšã³ã¹ãåæžå¹æ
- å®å šæ§ã®åäžãšäºæ 鲿¢
- å庫ã¬ã€ã¢ãŠãã®åºæ¬åå
- åç·ãšé çœ®ã®æé©å
- æªæ¥ã®æ¡åŒµæ§ãèæ ®ããèšèš
- å¹ççãªå庫ã¬ã€ã¢ãŠãã®èšèšææ³
- çŸç¶ã®ç©æµããã»ã¹ãšèª²é¡ã®ææ¡
- å šäœã¬ã€ã¢ãŠãã®æ±ºå®ãšãããã³ã°ãšãªã¢ã®èšèš
- ååä¿ç®¡å Žæãšäœæ¥ãšãªã¢ã®å²ãåœãŠ
- éè·¯ã®æé©é 眮ãšãããã¹ããŒã¹ã®æŽ»çš
- ãã©ãŒã¯ãªããã®éè·¯å¹ ãšå®å šæ§ã®ç¢ºä¿
- å ·äœçãªå庫ã¬ã€ã¢ãŠãäŸ
- çãå庫ã®ã¬ã€ã¢ãŠãäŸ
- Iååã¬ã€ã¢ãŠã
- Uååã¬ã€ã¢ãŠã
- å庫ã¬ã€ã¢ãŠã倿Žã®ã¿ã€ãã³ã°ãšæ³šæç¹
- ã¬ã€ã¢ãŠã倿Žã®æé©ãªã¿ã€ãã³ã°
- æ³çèŠå¶ãšå®å šåºæºã®éµå®
- 广çãªå庫ã¬ã€ã¢ãŠããèšèšããã
å庫ã¬ã€ã¢ãŠããšã¯
å庫ã¬ã€ã¢ãŠããšã¯ãå庫å ã«ãããä¿ç®¡ã¹ããŒã¹ãäœæ¥ã¹ããŒã¹ãéè·¯ãªã©ã®ç©ºéé 眮ãèšèšããããšã§ããå ·äœçã«ã¯ãæ£ãã©ãã¯ã®é 眮ããããã³ã°ãšãªã¢ã®äœçœ®ãå ¥è·ã»åºè·ãšãªã¢ã®é 眮ãªã©ã決å®ããŸãã
å¹ççãªå庫ã¬ã€ã¢ãŠãã¯ãäœæ¥åç·ãæ¹åããä¿ç®¡å¹çãé«ããäœæ¥è ã®å®å šã確ä¿ããããã«éåžžã«éèŠã§ãã
ã¬ã€ã¢ãŠãã¯æ±ãååã®çš®é¡ãéãäœæ¥å 容ããããŠå庫ã®åœ¢ç¶ãåºãã«ãã£ãŠæé©ãªãã®ãç°ãªããŸãããã®ãããããããã®å庫ã«åã£ãã¬ã€ã¢ãŠããæ€èšããããšãå¿ èŠãšãªããŸãã
ïŒïŒWMSïŒå庫管çã·ã¹ãã ïŒãšã¯
å庫ã¬ã€ã¢ãŠããæé©åããã¡ãªãã
å庫ã¬ã€ã¢ãŠããæé©åããããšã§ãç©æµæ¥åå šäœã®å¹çåãå³ããããŸããŸãªã¡ãªãããåŸãããŸããäž»ãªã¡ãªãããšããŠã次ã®3ã€ãæããããŸãã
- ç©æµå¹çã®æé©åãšäœæ¥å¹çåäž
- äœæ¥æéã®ççž®ãšã³ã¹ãåæžå¹æ
- å®å šæ§ã®åäžãšäºæ 鲿¢
ç©æµå¹çã®æé©åãšäœæ¥å¹çåäž
é©åãªã¬ã€ã¢ãŠãã¯ãå庫å ã®ç§»åè·é¢ãæå°éã«æããäœæ¥åç·ãã¹ã ãŒãºã«ããŸãããã®çµæãå ¥åºåº«ããããã³ã°ã梱å ãªã©ã®äœæ¥å¹çãåäžãã1æ¥ã®åŠçèœåãé«ããããã§ãããã
ããšãã°ãåºè·é »åºŠã®é«ãååãå ¥å£ä»è¿ã«é 眮ããããšã§ããããã³ã°äœæ¥ã®ç§»åè·é¢ãæžãããäœæ¥æéãççž®ã§ããŸãããŸããäœæ¥ã¹ããŒã¹ãåºã確ä¿ããããšã§ãäœæ¥è ãã¹ã ãŒãºã«ç§»åããäœæ¥å¹çãåäžãããããŸãã
äœæ¥æéã®ççž®ãšã³ã¹ãåæžå¹æ
äœæ¥å¹çã®åäžã¯ãäœæ¥æéã®ççž®ã«çŽçµããŸããäœæ¥æéãççž®ãããã°ã人件費ã®åæžã«ã€ãªãããŸãããŸããä¿ç®¡ã¹ããŒã¹ãå¹ççã«æŽ»çšããããšã§ãå庫ã®è³è²žè²»çšãæããããšãå¯èœã§ãã
åšåº«ç®¡çã®å¹çåã«ãã£ãŠãéå°ãªåšåº«ãæ±ãããªã¹ã¯ãæžãããåšåº«ç®¡çã³ã¹ããåæžã§ããŸãã
å®å šæ§ã®åäžãšäºæ 鲿¢
å庫å ã«ãããäºæ ã®ãªã¹ã¯ãäœæžããããšããã¬ã€ã¢ãŠãæé©åã®ã¡ãªããã§ããéè·¯å¹ ãé©åã«ç¢ºä¿ããããšã§ããã©ãŒã¯ãªãããã¯ãããšããäœæ¥è»äž¡ãšã®æ¥è§Šäºæ ã鲿¢ã§ããŸãã
æŽçæŽé ãããå庫ã¯ãäœæ¥è ã®èŠçãè¯å¥œã«ãã転åãèœäžãªã©ã®äºæ ãé²ããŸãããŸããé©åãªç §æãææ°ã確ä¿ããããšã§ãäœæ¥ç°å¢ãæ¹åããäœæ¥è ã®å¥åº·ãå®ãããšã«ãã€ãªããã§ãããã
å庫ã¬ã€ã¢ãŠãã®åºæ¬åå
å庫ã¬ã€ã¢ãŠããèšèšããéã«ã¯ã次ã®åºæ¬ååãèæ ®ããŸãããã
åç·ãšé çœ®ã®æé©å
å庫ã¬ã€ã¢ãŠãã®æ žå¿ã¯ãå¹ççãªåç·ãšæé©ãªé 眮ã«ãããŸããå ¥è·ããåºè·ãŸã§ã®æµããèæ ®ããåãšãªã¢ãé åºããé 眮ããããšã§ãäœæ¥å¹çãåäžããŸãã
äŸãã°ãå ¥è·ãæ€åãä¿ç®¡ããããã³ã°ã梱å ãåºè·ã®é ã«äžŠã¹ããšãç¡é§ãªç§»åãæžãããŸãããŸããååã®ç¹æ§ã«åãããä¿ç®¡æ¹æ³ããå転çã«å¿ããé 眮ã工倫ããããšã§ãã¹ããŒã¹ãæå€§éã«æŽ»çšã§ããŸããäœæ¥å¹çãšä¿ç®¡å¹çã®ãã©ã³ã¹ãåããªãããæé©ãªã¬ã€ã¢ãŠããç®æããŸãããã
æªæ¥ã®æ¡åŒµæ§ãèæ ®ããèšèš
çŸåšã®æ¥åéã ãã§ãªããå°æ¥çãªäºæ¥æ¡å€§ãæ¥åå 容ã®å€åã«ã察å¿ã§ãããããªã¬ã€ã¢ãŠãèšèšãéèŠã§ãã
ããšãã°ãå°æ¥çãªåšåº«éã®å¢å ãæ°ããªååã©ã€ã³ã®å°å ¥ãªã©ãæ³å®ãããããããã¹ããŒã¹ã確ä¿ããŠããå¿ èŠããããŸãããŸããã¬ã€ã¢ãŠã倿Žã«æè»ã«å¯Ÿå¿ã§ãããããå¯ååŒã®æ£ãã©ãã¯ãæ¡çšããã®ãæå¹ã§ãã
å¹ççãªå庫ã¬ã€ã¢ãŠãã®èšèšææ³
å¹ççãªå庫ã¬ã€ã¢ãŠããèšèšããã«ã¯ãæ¬¡ã®æé ãæèããŸãããã
çŸç¶ã®ç©æµããã»ã¹ãšèª²é¡ã®ææ¡
ãŸããçŸç¶ã«ãããç©æµããã»ã¹ã詳现ã«åæãã課é¡ãæç¢ºåããŸããå ·äœçã«ã¯ãå ¥è·ããåºè·ãŸã§ã®æµããäœæ¥å 容ãåãæ±ãååãåšåº«éãäœæ¥å¡æ°ãäœ¿çšæ©åšãªã©ãææ¡ããŸãããã
ãã®ããã§ãçŸåšã®ã¬ã€ã¢ãŠãã«ãããåé¡ç¹ãããšãã°åç·ã®éè€ãã¹ããŒã¹ã®ç¡é§ãäœæ¥ã®éå¹çæ§ãªã©ãæŽãåºããŸãããã®åæãããšã«ãæ¹åãã¹ããã€ã³ããæç¢ºåããå ·äœçãªç®æšãèšå®ããŸãã
å šäœã¬ã€ã¢ãŠãã®æ±ºå®ãšãããã³ã°ãšãªã¢ã®èšèš
ååº«å šäœã®ã¬ã€ã¢ãŠããæ±ºå®ããŸãããã®æ®µéã§ã¯ãIååãUååãLååãªã©ãåºæ¬çãªã¬ã€ã¢ãŠããã¿ãŒã³ãåèã«ããªãããå庫ã®åœ¢ç¶ãåºããåãæ±ãååãäœæ¥åç·ãªã©ãèæ ®ããŠæé©ãªã¬ã€ã¢ãŠããéžæããŸãã
ç¹ã«ãããã³ã°ãšãªã¢ã¯ãäœæ¥å¹çã«å€§ãã圱é¿ããéèŠãªãšãªã¢ã§ãããããã³ã°ã®é »åºŠãäœæ¥åç·ãèæ ®ããäœæ¥ããããäœçœ®ã«é 眮ããŸãã
ååä¿ç®¡å Žæãšäœæ¥ãšãªã¢ã®å²ãåœãŠ
ååããšã«é©åãªä¿ç®¡å Žæãå²ãåœãŠãŸããååã®ãµã€ãºãééãå転çãç¹æ§ãªã©ãèæ ®ããä¿ç®¡æ¹æ³ã決å®ããŸãããã
ããšãã°ãå転çã®é«ãååã¯ãããã³ã°ãšãªã¢ã«è¿ãå Žæã«é 眮ããééã®ããååã¯åºé¢ã«çŽæ¥çœ®ããªã©ãå¹ççãã€å®å šãªä¿ç®¡ãå¿ãããŸãããŸããäœæ¥ãšãªã¢ã¯äœæ¥å 容ã«åãããŠé©åãªåºãã確ä¿ããäœæ¥åç·ãèæ ®ããé 眮ã«ããŸãããã
éè·¯ã®æé©é 眮ãšãããã¹ããŒã¹ã®æŽ»çš
éè·¯ã¯ãäœæ¥å¹çãšå®å šæ§ã確ä¿ããããã«éèŠã§ãããã©ãŒã¯ãªãããäœæ¥å¡ãå®å šãã€ã¹ã ãŒãºã«ç§»åã§ãããããéè·¯å¹ ãé©åã«èšå®ããŸãããããŸããéè·¯ã®é 眮ã工倫ããããšã§ããããã¹ããŒã¹ãæå°éã«æããããŸãã
ããšãã°ãæ£ãã©ãã¯ã®é 眮ã工倫ããããšã§ãéè·¯ãå Œããä¿ç®¡ã¹ããŒã¹ã確ä¿ã§ããŸããããã«ãæ±ãå£éãªã©ã®ãããã¹ããŒã¹ãæå¹æŽ»çšããããã«ãå°çšã®æ£ãåçŽã¹ããŒã¹ãèšçœ®ããããšãæå¹ã§ãã
ãã©ãŒã¯ãªããã®éè·¯å¹ ãšå®å šæ§ã®ç¢ºä¿
ãã©ãŒã¯ãªããã䜿çšããå Žåã¯ãå®å šãªéè·¯å¹ ã確ä¿ããããšãç¹ã«éèŠã§ãããã©ãŒã¯ãªããã®æåã«å¿ èŠãªã¹ããŒã¹ãèæ ®ããéè·¯å¹ ãæ±ºå®ããŸãããã
ãŸãããã©ãŒã¯ãªããã®èµ°è¡ã«ãŒããæç¢ºåããäœæ¥å¡ãšã®æ¥è§Šäºæ ã鲿¢ããããã®å¯Ÿçãè¬ããå¿ èŠããããŸãã
ããšãã°ããã©ãŒã¯ãªããã®èµ°è¡ã«ãŒãã«èŠå衚瀺ãèšçœ®ããããäœæ¥å¡ãšãã©ãŒã¯ãªããã®åç·ãåé¢ããããããªã©ã®å·¥å€«ãæå¹ã§ãã
å ·äœçãªå庫ã¬ã€ã¢ãŠãäŸ
å庫ã®åºãã圢ç¶ãåãæ±ãååãäœæ¥å 容ã«ãã£ãŠãæé©ãªã¬ã€ã¢ãŠãã¯ç°ãªããŸããããã§ã¯ãå ·äœçãªå庫ã¬ã€ã¢ãŠãäŸãããã€ã玹ä»ããŸãã
çãå庫ã®ã¬ã€ã¢ãŠãäŸ
çãå庫ã§ã¯ãã¹ããŒã¹ãæå€§éã«æŽ»çšããªããã°ãªããŸããããã®ãããæ£ãã©ãã¯ã®é«ããé«ãããããéè·¯å¹ ãçãããããããªã©ã®å·¥å€«ãå¿ èŠã§ãããŸãããããã¹ããŒã¹ãæå°éã«æããããã«ãå£é¢ãæ±ãªã©ãæå¹æŽ»çšããããšãéèŠã§ãã
å¯ååŒã®æ£ãã©ãã¯ãæ¡çšããããšã§ãã¬ã€ã¢ãŠã倿Žã«æè»ã«å¯Ÿå¿ã§ããããã«ãªããã¹ããŒã¹å¹çãããã«é«ããããŸãã
Iååã¬ã€ã¢ãŠã
Iååã¬ã€ã¢ãŠãã¯ãå ¥è·ãšãªã¢ãšåºè·ãšãªã¢ãå庫ã®äž¡ç«¯ã«é 眮ãããã®éãä¿ç®¡ãšãªã¢ãšããã¬ã€ã¢ãŠãã§ããååã®æµããäžçŽç·ã«ãªããããäœæ¥åç·ãæçã«ãªããç§»åè·é¢ãæå°éã«æããããŸãã
ãã®ããããããã³ã°äœæ¥ã®å¹çåã«ã€ãªãããäœæ¥æéã®ççž®ãæåŸ ã§ããŸãã
ãã ããäœæ¥å¡ããã©ãŒã¯ãªããã®åç·ã亀差ããå¯èœæ§ãé«ããããå®å šç®¡çã«ã¯æ³šæãå¿ èŠã§ãã
Uååã¬ã€ã¢ãŠã
Uååã¬ã€ã¢ãŠãã¯ãå ¥è·ãšãªã¢ãšåºè·ãšãªã¢ãåãåŽã«é 眮ããä¿ç®¡ãšãªã¢ãUååã«é 眮ããã¬ã€ã¢ãŠãã§ããIååã¬ã€ã¢ãŠãã«æ¯ã¹ãŠãäœæ¥åç·ã¯é·ããªããŸãããã¹ããŒã¹å¹çã«åªããŠããŸãã
ãŸããäœæ¥å¡å士ãé¢åãããããªã¹ã¯ãæžãããå®å šæ§ãé«ãŸããŸãããããã³ã°ãšãªã¢ãäž¡åŽã«é 眮ããããšã§ãäœæ¥å¹çãåäžãããããšãå¯èœã§ãã
å庫ã¬ã€ã¢ãŠã倿Žã®ã¿ã€ãã³ã°ãšæ³šæç¹
å庫ã¬ã€ã¢ãŠãã¯ãäžåºŠæ±ºãããçµããã§ã¯ãããŸãããæ¥åã®æ¡å€§ãå€åã«åãããŠã宿çã«èŠçŽããæ¹åããŠããå¿ èŠããããŸãã
ã¬ã€ã¢ãŠã倿Žã®æé©ãªã¿ã€ãã³ã°
ã¬ã€ã¢ãŠã倿Žãè¡ãã¿ã€ãã³ã°ãšããŠã¯ã次ã®ãããªå ŽåãèããããŸãã
é ç® | 説æ |
---|---|
æ¥åéã®å¢å ãæžå° | åæ±éãå¢å ãä¿ç®¡ã¹ããŒã¹ãäžè¶³ããŠããããããã¯ãã®å察ã«ãæ¥åéãæžå°ãã¹ããŒã¹ã«äœè£ãã§ããå Žåãªã©ã¯ãã¬ã€ã¢ãŠã倿Žãæ€èšããã¿ã€ãã³ã°ã§ãã |
æ°ååã®å°å ¥ | ãµã€ãºã圢ç¶ãä¿ç®¡æ¹æ³ãç°ãªãæ°ååãå°å ¥ããéã¯ãæ¢åã®ã¬ã€ã¢ãŠãã§ã¯å¯Ÿå¿ã§ããªãå¯èœæ§ããããŸããæ°ååã®ç¹æ§ã«åãããã¬ã€ã¢ãŠã倿Žãå¿ èŠãšãªããŸãã |
äœæ¥å¹çã®äœäž | äœæ¥åç·ãè€éåãç§»åè·é¢ãå¢å ããŠããããããã³ã°ãã¹ãå¢ããŠãããªã©ãäœæ¥å¹çãäœäžããŠããå Žåã¯ãã¬ã€ã¢ãŠããèŠçŽãå¿ èŠããããŸãã |
äºæ ã®çºç | å庫å ã§äºæ ãçºçããå Žåããã®åå ãåæããã¬ã€ã¢ãŠãã«åé¡ããªããã確èªããå¿ èŠããããŸããå®å šæ§ãåäžãããããã®ã¬ã€ã¢ãŠã倿Žãå¿ èŠãšãªãå ŽåããããŸãã |
ã¬ã€ã¢ãŠã倿Žãè¡ãéã«ã¯ãæ¥åãžã®åœ±é¿ãæå°éã«æããããã«ãç¹å¿æãé¿ããŠãæ¯èŒçæ¥åéã®å°ãªãææãéžã³ãŸãããããŸããäºåã«ååãªèšç»ãç«ãŠãé¢ä¿éšçœ²ãšã®é£æºãå¯ã«ããããšã倧åã§ãã
æ³çèŠå¶ãšå®å šåºæºã®éµå®
å庫ã¬ã€ã¢ãŠãã®å€æŽãè¡ãéã«ã¯ãæ¶é²æ³ã建ç¯åºæºæ³ãªã©ã®æ³çèŠå¶ãéµå®ããªããã°ãªããŸãããããšãã°ãéè·¯å¹ ãé¿é£çµè·¯ã®ç¢ºä¿ãæ¶ç«èšåã®èšçœ®ãªã©ãæ³ä»€ã§å®ããããåºæºãæºããå¿ èŠããããŸãã
ãŸããåŽåå®å šè¡çæ³ã«åºã¥ããäœæ¥å¡ã®å®å šã確ä¿ããããã®æªçœ®ãè¬ããªããã°ãªããŸãããå ·äœçã«ã¯ããã©ãŒã¯ãªããã®å®å šå¯Ÿçãé«æäœæ¥ã®å®å šå¯Ÿçãç §æã®èšçœ®ãªã©ãäœæ¥ç°å¢ã®å®å šæ§ã確ä¿ããããã®å¯Ÿçãè¬ããå¿ èŠããããŸãã
æ³çèŠå¶ãå®å šåºæºãéµå®ããããšã§ãäºæ ãçœå®³ãæªç¶ã«é²ããå®å šãªå庫éå¶ãå®çŸããŸãããã
广çãªå庫ã¬ã€ã¢ãŠããèšèšããã
å庫ã¬ã€ã¢ãŠããšã¯ãå庫å ã«ãããä¿ç®¡ã¹ããŒã¹ãäœæ¥ã¹ããŒã¹ãéè·¯ãªã©ã®ç©ºéé 眮ãèšèšããããšã§ããæé©åãããå庫ã¬ã€ã¢ãŠãã¯ãç©æµå¹çã®åäžãã³ã¹ãåæžããããŠå®å šæ§ã®ç¢ºä¿ãšãã£ãå€ãã®ã¡ãªããããããããŸãã
å庫ã¬ã€ã¢ãŠããèšèšããããã§éèŠãªã®ã¯ãåç·ãšé çœ®ã®æé©åããããŠå°æ¥ã®æ¡åŒµæ§ãèæ ®ããããšã§ãããããã®èŠçŽ ããã©ã³ã¹è¯ãèšèšããããšã§ãéãããã¹ããŒã¹ãæå€§éã«æŽ»çšããã¹ã ãŒãºãªäœæ¥ã®æµããå®çŸã§ããŸãã
ãã®çµæãäœæ¥æéã®ççž®ãã³ã¹ãåæžããããŠåŸæ¥å¡ã®å®å šç¢ºä¿ãšãã£ã广ãæåŸ ã§ããŸãããã²ããã®èšäºã§ç޹ä»ããå 容ãåèã«ãèªç€Ÿã®ååº«ã«æé©ãªã¬ã€ã¢ãŠããæ§ç¯ããããå¹ççãªç©æµäœå¶ãç®æããŸãããã