工場レイアウトを最適化するには?生産性を高めるポイント
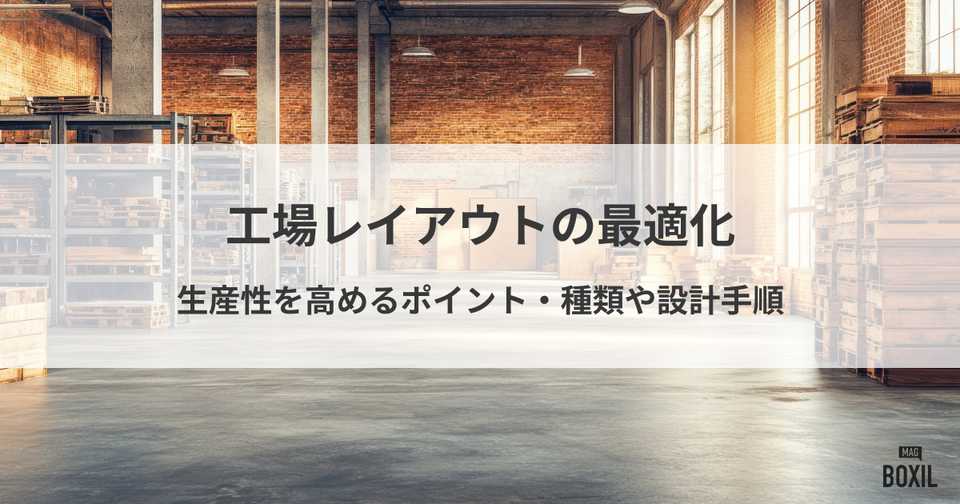
目次を閉じる
工場レイアウトとは
工場レイアウトとは、工場における機械設備や作業員などの配置を表します。これは単なる配置ではなく、生産効率の最大化、作業員の安全性、製品の品質維持などを考慮した戦略的な配置です。
工場には大きく分けて、装置型工場と組立型工場があります。
装置型工場
装置型工場は、製鉄や化学プラントのように大型の装置を中心に配置する工場です。一度レイアウトを決めると変更が難しいため、初期段階での綿密な計画が重要となります。
組立型工場
組立型工場は、自動車工場や電子機器工場のように部品を組み立てて製品を製造する工場です。比較的レイアウトの変更が容易であり、生産状況に合わせて柔軟に変更できます。
最適なレイアウト
最適なレイアウトは、これらの工場の種類、製品の種類、生産量、作業工程など、工場の状況によって異なります。
効率的な工場レイアウトは、スムーズな生産活動に不可欠であり、工場の生産性向上につながる重要な要素です。
工場レイアウトの種類
工場レイアウトは、製品の種類や生産量、製造工程などによって最適な配置が変わります。代表的な種類として、ジョブショップ型、ライン型、セル型、据え置き型が挙げられます。
ジョブショップ型
ジョブショップ型は、機能別に機械設備を配置するレイアウトです。たとえば、旋盤、フライス盤、研磨機など、同じ種類の機械をまとめて配置します。
この方式は多品種少量生産に適しており、さまざまな製品を柔軟に生産できます。作業者は複数の機械を操作しなければならず、高いスキルが必要です。そのため、多能工化を目指す場合にも適しています。
デメリットは製品の流れが複雑になりやすいことで、運搬の効率が悪くなる場合があります。
ライン型
ライン型は、製品の製造工程順に機械設備を配置するレイアウトです。流れ作業で製品を効率的に生産できるため、大量生産に向いています。自動車工場や家電工場などでよく見られます。
製品の流れが明確で、運搬の効率が良いのが特徴です。ただし、多品種少量生産には不向きであり、ラインの一部が停止すると全体の生産がストップするリスクがあります。
セル型
セル型は、複数の機械と作業者で構成される生産セルを配置するレイアウトです。各セル内で製品の組立や加工が完結するように配置することで、多品種少量生産と多量生産の両方に対応できます。比較的新しいレイアウト方式であり、柔軟性と効率性を兼ね備えている点が特徴です。
セル型では作業者間の連携が重要となり、チームワークを重視した作業環境が求められます。これにより、効率的な生産体制を構築できます。
据え置き型
据え置き型は、大型の製品や移動が困難な製品を製造する場合に採用されるレイアウトです。たとえば、造船や航空機製造などが該当します。製品が定位置に据え置かれ、作業者や機械が製品の周りを移動して作業を行います。
製品の移動が不要で、大型製品の製造に適したレイアウトです。しかし、広い作業スペースが必要となり、レイアウトの変更が難しいという特徴を持ちます。
工場レイアウトを最適化する6つのポイント
工場レイアウトを最適化することで、生産効率の大幅な向上が期待できます。最適化のための重要なポイントを6つ紹介します。
ポイント1. 動線の最適化
動線の最適化とは、人や物が工場内を移動する経路を効率化することです。無駄な移動を減らし、スムーズな流れを作ることで、作業効率の向上が可能です。
動線が最適化されると、作業時間の大幅な短縮や作業者の負担軽減が期待できます。また、工場内での事故リスクを減らす効果もあります。
ポイント2. 作業効率の向上
作業効率の向上とは、作業者が無駄なく効率的に作業できる環境を整えることです。作業スペースの確保や適切な設備の配置などが重要です。
作業効率が向上することで、生産性はもちろん、従業員のモチベーション向上にもつながります。結果として、製品の品質向上も期待できます。生産体制の強化に貢献するでしょう。
ポイント3. 保管場所の最適化
保管場所の最適化とは、原材料や製品の保管場所を適切に配置し、必要なときにスムーズに取り出せるようにすることです。在庫管理の効率化にもつながります。
保管場所を最適化することで、在庫管理コストの削減や、必要なものを迅速に供給できる体制の構築が可能です。
ポイント4. エリア分け
エリア分けとは、工場内の部門や作業エリアを適切に配置することです。作業の流れや連携を考慮し、効率的な配置を実現します。
適切なエリア分けを行うことで、部門間の連携がスムーズになり、情報伝達や物の流れが円滑になります。
ポイント5. 安全性の確保
安全性の確保とは、作業者が安全に作業できる環境を整えることです。危険な場所への立ち入り制限や、安全設備の設置などが重要です。
安全性を確保することで、労働災害のリスクを大幅に低減できます。従業員が安心して働ける環境は、生産性の向上にもつながります。
ポイント6. 拡張性・柔軟性
拡張性・柔軟性とは、将来的な生産量の増加や製品の変化に対応できるレイアウトにすることです。変化に強い工場を作るために重要な要素です。
拡張性・柔軟性を持たせることで、将来的な事業拡大や製品の変化に柔軟に対応できます。これにより、長期的な視点での工場運営が可能になります。
工場レイアウト設計の手順
工場レイアウト設計は、生産効率や作業安全性に大きく影響する重要なプロセスです。次のような手順を踏むことで、より効果的なレイアウトを実現できます。
- 現状分析
- P-Q分析
- 物の流れの分析
- アクティビティ分析
- スペース分析
- レイアウト案の作成と評価
- シミュレーションの活用
1. 現状分析
現状分析では、現在の工場の状況を詳細に把握します。具体的には、生産量、製品の種類、使用している設備、作業者の配置、動線などを調査します。図面やデータ、現場調査などを活用し、客観的な情報を収集しましょう。
現状分析を行うことで、改善すべき点や課題が明確になります。
2. P-Q分析
P-Q分析では、生産する製品の種類(Product)と数量(Quantity)を分析します。具体的には、どの製品がどれだけ生産されているのかをデータ化し、製品ごとの生産量や生産頻度を把握します。これにより、主力製品や多品種少量生産の製品群などの特定が可能です。
P-Q分析を行うことで、どの製品に重点を置いたレイアウトにすべきかが明確になります。たとえば、大量生産される製品はライン生産方式に適しているというように、適切なレイアウト方式を選択するための情報が得られます。
3. 物の流れの分析
物の流れの分析では、原材料の入荷から製品の出荷までの物の流れを追跡し、可視化します。具体的には、各工程間での物の移動距離、運搬方法、停滞時間などを調査し、流れ図を用いて整理しましょう。
物の流れを分析することで、無駄な運搬や停滞が発生している箇所を特定できます。効率的な物の流れを実現するためのレイアウトを検討するうえで不可欠な情報となります。
4. アクティビティ分析
アクティビティ分析では、工場内で行われている作業内容(アクティビティ)を分析します。具体的には、各作業に必要なスペース、設備、作業者、関連部署などを洗い出し、アクティビティ間の関連性を明確にしましょう。アクティビティ相互の関係を図式化したアクティビティ相互関係図が用いられます。
アクティビティ分析を行うことで、作業間の連携や流れを考慮したレイアウトを検討できます。部門間の配置や設備の配置などを最適化することで、作業効率の向上が可能です。
5. スペース分析
スペース分析では、工場全体のスペースと各作業に必要なスペースを分析します。工場全体の面積、各設備の占有面積、作業スペース、通路スペースなどを測定し、必要なスペースを確保できているかを確認しましょう。
スペース分析を行うことで、スペースの過不足を把握し、適切な広さの作業スペースや通路を確保できます。作業効率の向上だけでなく、安全な作業環境の確保にもつながります。
6. レイアウト案の作成と評価
これまでの分析結果をもとに、複数のレイアウト案を作成します。図面や3Dモデルなどを用いてレイアウトを具体的に表現し、各案のメリット・デメリットを比較検討しましょう。
レイアウト案を比較検討することで、最適なレイアウトを選択できます。作業効率、安全性、拡張性など、複数の視点から評価することで、よりバランスの取れたレイアウトを選べるでしょう。
7. シミュレーションの活用
作成したレイアウト案をシミュレーションすることで、実際の運用を想定した検証を行いましょう。コンピュータシミュレーションを用いて、物の流れ、作業者の動き、設備の稼働状況などを再現し、問題点や改善点を見つけ出します。
シミュレーションを活用することで、実際に工場を稼働させる前に問題点を発見し、改善できます。これにより、導入後のトラブルを未然に防ぎ、スムーズな立ち上げが可能です。
適切な工場レイアウトで効率的な生産体制を
工場レイアウトは生産効率、作業安全性、従業員の働きやすさに影響する重要な要素です。適切なレイアウトは、無駄な作業や移動を削減し、工場の潜在能力を引き出します。
適切な工場レイアウトにより、動線最適化による移動時間短縮、作業効率向上による作業時間削減、保管場所最適化による在庫管理効率化など、多岐にわたる効果が期待できます。これらの効果は相乗効果によって生産体制を飛躍的に向上させるでしょう。