生産方式とは?4つの種類とメリット・デメリット、適したケース、選び方
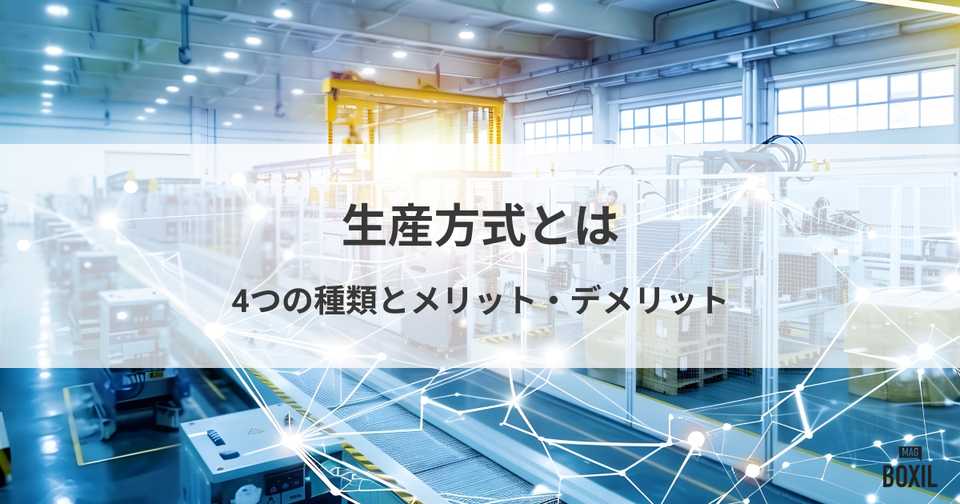
目次を閉じる
生産方式とは
生産方式とは、製品やサービスを効率的に生産するための方法や手順を体系化したものです。原材料の調達から始まり、設計、製造、検査、出荷に至るまで、生産に関わるすべての工程が含まれます。
生産方式の目的は、品質の向上、コストの削減、納期の遵守、そして顧客満足度の向上です。企業は、市場のニーズや自社の経営戦略に合わせて、最適な生産方式を採用する必要があります。
近年では、多様化する顧客のニーズに対応するため、従来の大量生産方式に加え多品種少量生産や個別受注生産など、さまざまな生産方式が導入されています。
適切な生産方式を導入することで、企業は生産性を向上させ、競争力を強化できるでしょう。
生産方式の種類
企業の規模や製品の種類、顧客のニーズによって、最適な生産方式は異なります。代表的な生産方式には次の4つが挙げられます。
- ライン生産方式
- ロット生産方式
- 個別生産方式
- セル生産方式
ライン生産方式
ライン生産方式とは、生産ラインを細かな作業に分け、流れ作業で生産する方式です。ライン上を進むにつれ加工も進み、製品が完成していきます。
それぞれの作業者が工程ごとに専門化された作業を担当することで、効率的に大量生産を行えます。
メリット | デメリット |
---|---|
・生産性が高い ・コストが低い ・品質が安定しやすい |
・柔軟性に欠ける ・作業者のモチベーションが低下しやすい ・トラブル発生時の影響が大きい |
ライン生産方式では、作業の標準化や分業化によるメリットを得られます。一人あたりの作業時間を短縮するほか、製品1つあたりのコスト削減、品質の均一化などを実現されます。
また、大量生産には適していますが、製品の種類や生産量の変更に対応しにくい側面も避けて通れません。単調な作業のくり返しとなるため、作業者のモチベーションが低下しやすい点も課題です。
そして、ラインのどこかの工程でトラブルが発生すると、全体の生産が停止してしまうリスクもあります。
ロット生産方式
ロット生産方式とは、ある程度のまとまった量(ロット)で製品を生産する方式です。たとえば、同じ原料や部品を使う製品をまとめて生産することで、段取り替えの手間を減らし、効率的に生産できます。
メリット | デメリット |
---|---|
・段取り替えの回数を減らせる ・ライン生産方式に比べて多様な製品に対応できる ・在庫管理がしやすくなる |
・在庫を抱えるリスクがある ・需要予測が難しい ・ライン生産方式に比べて生産性が低い |
ロット生産方式は、同じ製品をまとめて生産できるため、製造ラインの段取り替え回数を減らし、生産効率の向上を目指せます。
ライン生産方式に比べて、多様な製品の生産に対応できるメリットがあり、ある程度の量の在庫を持てるため、急な需要の変化にも対応しやすいです。
一方で、ある程度の在庫を抱えるため、在庫管理コストや売れ残った場合のリスクが大きく、ライン生産方式に比べると生産性が低いです。また、適切なロットサイズを見積もるためには、正確な需要予測が求められます。
個別生産方式
個別生産方式とは、顧客の注文に応じて、製品を一つひとつ個別に生産する方式です。オーダーメイドスーツや注文住宅などが、この方式に該当します。
メリット | デメリット |
---|---|
・顧客のニーズに合わせた製品を提供できる ・高付加価値製品の生産に適している ・多様な製品に対応できる |
・生産コストが高い ・納期が長くなりやすい ・生産管理が複雑になる |
個別生産方式では、顧客のニーズに合わせて、多様な製品を生産できるため、顧客の要望を直接反映した製品を製造でき、顧客満足度も高められるでしょう。
高度な技術や特別な素材を必要とする製品など、高付加価値製品の生産にも適した方式です。
個別生産方式では、製品ごとに設計や製造工程が異なるため、生産コストが高くなる傾向にあります。一つひとつの製品を丁寧に作る必要があるため、納期が長くなりやすいです。
納期が長くなれば受注から入金までの期間も長くなり、キャッシュフローの悪化が懸念されます。また、多様な製品を管理する必要があるため、生産管理が複雑になる側面もあります。
セル生産方式
セル生産方式とは、作業者を少人数のグループ(セル)に分け、各セルが製品の完成までを担当する生産方式です。それぞれのセルが、複数の工程を担当することで、作業者一人ひとりの責任感やモチベーションを高められます。
メリット | デメリット |
---|---|
・作業者のモチベーション向上 ・多能工化による人材育成 ・柔軟な生産体制 |
・ライン生産方式に比べて生産効率が低い ・セル間の連携が難しい ・多能工化のための教育コストがかかる |
セル生産方式では、作業者が製品の完成まで関わることで、責任感や達成感を持ちやすくなります。複数の工程を経験することで、作業者のスキルアップや多能工化も促進できます。
また、セルごとに独立して作業を行うため、生産量の調整や製品の変更など柔軟な対応が可能です。
セル生産方式はライン生産方式に比べて、生産効率が低いです。また、各セルが独立して作業を行うため、セル間の連携が難しくなることも。作業者を多能工化するためには、教育コストや時間もかかります。
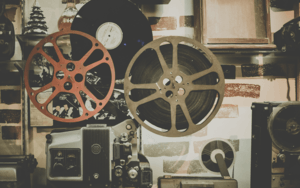
生産時期による分類
生産方式は、製品を生産するタイミングによっても分類できます。見込み生産と受注生産の2つについて解説していきます。
生産方式 | メリット | デメリット |
---|---|---|
見込み生産 | ・顧客の要望に迅速に対応できる ・計画的な生産により、コスト削減が可能 ・大量生産によるスケールメリット |
・需要予測が外れた場合、在庫過多になるリスクがある ・在庫保管コストが発生する ・顧客の詳細なニーズには対応できない |
受注生産 | ・顧客のニーズに最適な製品を提供できる ・無駄な在庫を抱えるリスクがない ・多品種少量生産に対応しやすい |
・納期が長くなりやすい ・生産計画を立てにくい ・急な注文に対応できない場合がある |
見込み生産
見込み生産とは、将来の需要を見込んであらかじめ製品を生産しておく方式です。この方式は、市場に安定した需要がある製品に適しています。
見込み生産では、あらかじめ製品を生産することで、顧客からの注文にすぐに対応できます。また、計画的に生産をするため、生産コストを削減しやすいです。大量生産を行うことで、材料費や製造コストを抑えられます。
見込み生産では、需要予測が重要であることの裏返しで、もし予測が外れてしまうと売れ残りが発生し、在庫過多になるリスクをはらんでいます。また、製品を保管するための倉庫や管理費用などのコストも発生するでしょう。
顧客のニーズが多様化している現代においては、あらかじめ生産した製品が顧客の要望と完全に一致しない可能性も高いです。
受注生産
受注生産とは、顧客から注文を受けてから製品の生産を開始する方式です。この方式は、顧客のニーズが多様化している現代において、注目されています。
受注生産では、注文を受けてから生産を開始するため、納期が長くなりやすいです。納期が長くなれば入金までの期間も長くなり、キャッシュフロー悪化のリスクもあるでしょう。
また、需要を予測することが難しいため、生産計画を立てるのも難しいです。生産能力を超える注文があった場合、対応できない可能性もあります。
自社に合う生産方式を選ぶPQ分析とは
PQ分析とは、Product(製品)とQuantity(数量)の関係を分析することで、最適な生産方式を決定する手法です。具体的には、製品の種類と生産量をグラフ化し、それぞれの製品がどの生産方式に適しているかを判断します。
PQ分析の進め方
PQ分析は、次の手順で進めます。
- データ収集:一定期間における製品の種類と生産量、売上などのデータを集めます
- グラフ作成:横軸に製品の種類、縦軸に生産量をとったグラフを作成します
- 分析:グラフから、製品を次の3つのグループに分類します
分類 | 内容 |
---|---|
Aグループ | 生産量が多い製品群。ライン生産方式が適しています。 |
Bグループ | 生産量が中程度の製品群。ロット生産方式やセル生産方式が適しています。 |
Cグループ | 生産量が少ない製品群。個別生産方式が適しています。 |
生産方式の選び方
PQ分析の結果を参考に、次の点を考慮して最終的な生産方式を決定します。
項目 | 内容 |
---|---|
製品の特性 | 製品の種類やサイズ、形状、品質レベルなど |
生産量 | 各製品の生産量や需要変動 |
コスト | 原材料や設備にかかる費用 |
納期 | 顧客が求める納期 |
企業の戦略 | 企業の経営方針や競争戦略 |
PQ分析は、あくまで1つの指標であり、最終的な生産方式の決定は、上記の要素を総合的に判断して行う必要があります。
PQ分析を活用し、自社に合う生産方式を選ぼう
企業の規模や製品の種類、顧客のニーズによって、最適な生産方式は異なります。それぞれの生産方式のメリットとデメリットを理解したうえで、自社に合ったものを選択しましょう。生産方式を決める際には次のような流れを行います。
- 現状の生産システムを分析する
- PQ分析を実施し、製品群ごとの特性を把握する
- 各生産方式のメリット・デメリットを理解する
- 企業の戦略や市場の動向を考慮する
- 必要に応じて複数の生産方式を組み合わせる
PQ分析を活用することで、製品の種類と生産量の関係を可視化し、どの生産方式が適しているかを判断できます。しかし、PQ分析はあくまでも1つの指標です。
最終的な生産方式の決定は、製品の特性、生産量、コスト、納期、企業の戦略など、さまざまな要素を総合的に判断して行う必要があります。
ぜひ今回の内容を参考に、最適な生産方式を導入し、生産性向上を目指しましょう。
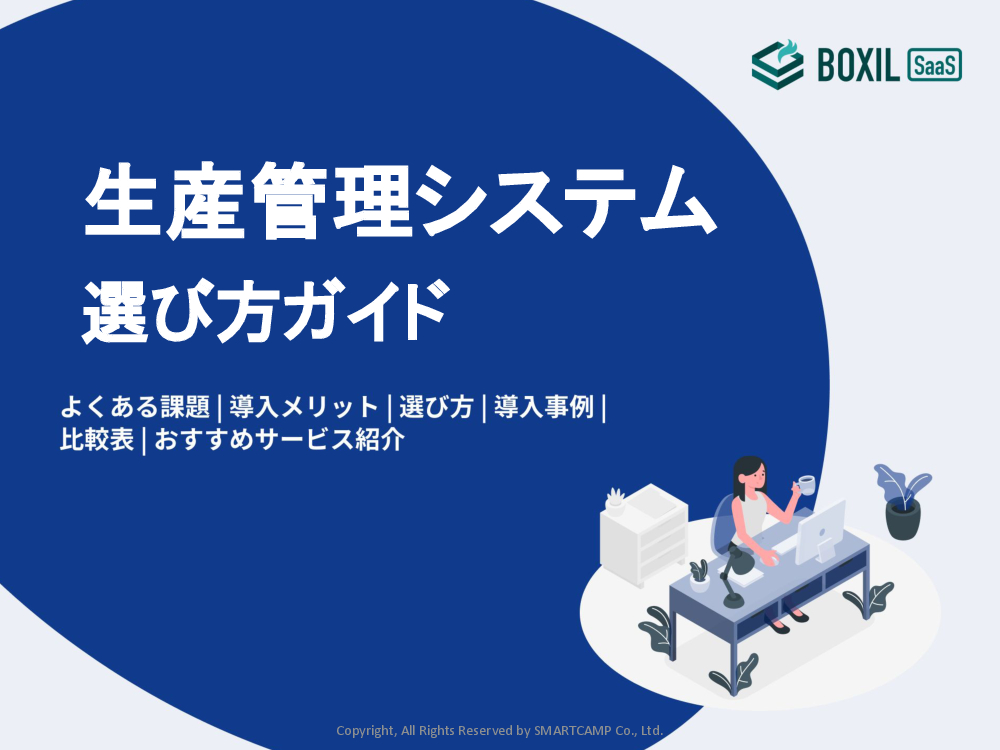