生産管理のQCDとは? 品質・コスト・納期を効果的に管理する方法

目次を閉じる
生産管理におけるQCDの重要性とは
QCDとは「品質(Quality)」「コスト(Cost)」「納期(Delivery)」の3要素のことで、生産管理において重要な要素です。QCDを満たすことで企業の利益を最大化させ、顧客満足度の向上につながります。品質、コスト、納期はそれぞれ3すくみであることが特徴です。
納期やコストを控えすぎると、品質低下とクレームの原因になります。一方、コストは直接的に利益に影響しますが、コストが高すぎると利益が減少し、販売価格が高騰して消費者の購入意欲を低下させる可能性があります。
納期を守ることも不可欠で、遅れればたとえ製品が優れていても販売のチャンスを失いやすいです。このように、QCDは相互に影響を及ぼし合うため、一つを追求しすぎると他にしわ寄せが生じます。効果的な在庫管理のためには、QCDのバランスを見極めることが重要です。
>>QCDとは?品質やコストの優先順位 | 派生語QCDS・QCDSE
社会的責任「CSR」とQCDの関連性
企業はQCDを追求して利益を最大化させることが目的ですが、近年はCSRへの取り組みも求められています。CSRとは「Corporate Social Responsibility」の頭文字を取ったもので、「企業の社会的責任」といった意味です。
企業は利益を追求する活動をするにあたって、環境や次世代へ配慮する責任があります。社会的に貢献するだけでなく、環境や人権、企業に関係する人間が幸福になるための活動が必要です。
CSRに配慮するためにQCDは次のような派生型が生まれ、自社に合った取り組みを行っています。
派生型QCDの種類 | 取り組み内容 |
---|---|
EQCD | 環境に配慮したQCD |
SQCD | 安全に配慮したQCD |
QCDS | 顧客対応に配慮したQCD |
QCDF | 柔軟性を重視したQCD |
生産管理におけるQCDに基づく改善手法
生産管理を改善するにはQCDに基づいた取り組みを行うことが重要です。品質管理、コスト管理、工数管理の観点からどのように生産管理を改善するか詳しく解説します。
品質管理とQCD
品質管理は顧客満足度の向上や長期的な企業成長につながるため、QCDの中でもっとも重要な要素で、一定の品質を担保する役割があります。低コストで納期どおりに製品を顧客の元へ届けられたとしても、品質が悪ければ顧客満足度の向上につながらず、場合によっては顧客の信頼を失いかねません。
一定の品質を保ち、合格基準を達成させるための手法は次のとおりです。
- 作業のマニュアル化
- 設備の管理
- 検品の徹底
作業をマニュアル化することで、従業員の練度にかかわらず一定の製品を生産できます。また、製品を生産する設備を見直し、メンテナンスを行うことで不良品の生産を防げます。また、検品を徹底することで不良品の出荷防止が可能です。
コスト管理とQCD
コスト管理は一定の品質を保ちながら製品を完成させるための予算を決める取り組みです。原材料費や人件費、設備にかかる経費を計算します。利益の向上や競合他社との競争力維持のためにコスト管理は重要です。適切な原材料費や人件費を設定したり、設備に投資したりすることで生産性の向上に役立ちます。
代表的なコスト管理は次のとおりです。
- 消耗品のコスト削減
- 在庫の削減
- 古い設備を入れ替える
原材料費や人件費の大幅なコスト削減をしてしまうと、品質が落ちたり従業員の負荷が高まったりする可能性があります。したがって、消耗品のような製品の品質に影響を与えにくいものからコスト削減するといいでしょう。
また、在庫を抱えたままだと維持費用や廃棄費用が増加します。また、古い設備やシステムは業務効率が悪くなり、ランニングコストの増加につながる恐れがあるため、新しいシステムに変更するべきケースもあります。
工数管理とQCD
工数管理は納期を守るために必要な管理です。作業に必要な工程と数をピックアップし、どれくらいの時間がかかるかを計算してスケジュールを立てます。また、生産が開始されたらスケジュールどおりに進行しているかの確認も重要です。
スケジュールが早すぎたら顧客への不信感を抱かせたり、保管費用の高騰につながったりする恐れがあります。また、スケジュールが遅すぎても顧客の信頼低下を招く恐れがあるため、設備の見直しといった対策が必要です。
工数を削減するためには業務の標準化や工数の改善といった手法が効果的です。業務を標準化することで、作業者による業務のバラつきを一定にできます。また、工程を改善することでスケジュールどおりに進められ、一定の品質を保つことにもつながります。
QCD導入によって得られるメリット
QCD導入によって得られるメリットは次のとおりです。
- 品質向上による顧客満足度の向上
- コスト削減による利益率向上
- 納期遵守による信頼性の向上
それぞれ詳しく解説します。
品質向上による顧客満足度の向上
QCDを導入することで、コストや納期のバランスを取りながら一定の品質を担保できるため、顧客満足度の向上につながります。
納期どおりに製品を顧客に届けられたとしても品質が悪ければ顧客の信頼は得られません。顧客の信頼を失えば次回の商品を購入してくれなくなってしまい、長期的な利益につながらなかったり、ブランディングの低下につながったりする恐れがあります。
QCD導入することで、一定の品質を保ちながらコストを削減し、納期どおりに製品を顧客へ届けられます。そのため、顧客の信頼獲得が可能です。顧客の信頼を得られればリピーター獲得につながるため、新商品を販売した際の利益が見込みやすくなります。
また、顧客がファンになってくれればSNSでの口コミにつながりやすく、自社や製品のブランディング強化が可能です。さらに、顧客がSNSや口コミをしてくれるのであれば、余分な宣伝費の削減ができます。宣伝にかける費用を削減できれば大幅なコスト削減につながります。
コスト削減による利益率向上
QCDを導入することでコスト削減につながり、利益の向上が可能です。製品の品質が高くても原材料費や設備費といったコストが大幅にかかっていたら利益は上がりません。したがって、一定の品質を保ちながらコストをできる限り下げることが利益率向上には重要です。
たとえば、ムダに行っていた工程を削減するだけでもコストの削減は可能です。必要のない工程を削減することで、その工程にかけていた人材と時間を削減できます。削減した人材と時間は他の業務に充てられたり、設備投資ができたりするため、生産効率や利益率の向上につながります。
コストを削減には設備稼働率、在庫回転率、廃棄率、残業時間といったデータの収集が重要です。データを収集し、不要なコストがかかっていないかの見直しを図ることで、品質や納期を守りながらコスト削減できます。
納期遵守による信頼性の向上
QCDを導入することで決められた納期を守りやすくなり、顧客からの信頼を得られるようになります。製品がいかに優れていたとしてもスケジュールどおりに手元に届かなかったら顧客は予定が立てられません。
たとえば、顧客が飲食販売の仕入れのために注文していたにもかかわらず、商品が届かなかったら販売機会を失ってしまい、信用を失うでしょう。
納期を守るためには、納期までの工数やかかる時間を算出し、スケジューリングをすることが重要です。また、スケジュールどおりに生産業務が進んでいるか、トラブルが起きていないかを常にチェックする必要があります。遅れが生じた際は、生産工数を見直したりボトルネックになっている工程にリソースを追加したりといった対策が求められます。
生産管理のQCD改善方法
生産管理におけるQCDの改善方法は次のとおりです。
- 課題の明確化
- 改善策の実施
- 効果の検証
それぞれ詳しく解説します。
課題の明確化
QCDを改善するためには、まず課題を明確化する必要があります。生産業務を行っている現場の意見をヒアリングし、現状はどのような課題があるのかを正確に抽出します。また、ヒアリングした情報に加えてデータ分析も必要です。返品数やクレーム数、設備稼働率といった数値を整理することで課題の把握ができるようになります。
また、それぞれの生産工程がどのように連動しているかを確認することも重要です。業務ワークフローや進捗状況を確認して目標数値に達成していない、ボトルネックになっている部分がないかを発見することで、改善すべきポイントが見えるようになります。
改善策の実施
課題を明確化したら改善計画を立案し、実行に移しましょう。改善計画を実行に移す際は課題解決の優先順位をつけるのが重要です。また、コストや納期、顧客満足度、返品数といった具体的な指標を用いることで具体的な改善策を立てられます。
たとえば、コストが高額になりすぎていたら削減できるコストがないかを見直したり、返品数やクレームが多かったら材料の見直しや返品が出やすい工程の見直しを行ったりです。
このように、課題を明確にして改善したら具体的にどのように変わったかを確認できるようにするのが重要です。
効果の検証
改善策を実施したらどのような効果があったのかを検証し、成功と失敗の要因を特定します。効果検証の際は指標から得られたデータだけでなく、現場からヒアリングするといった数値化できない点からも検証するのが重要です。
また、検証の際に数値化できる課題に関しては可能な限り数値化するのが重要です。KPIを設定することで目標に対してどの程度達成できたのか、目標達成のために行った改善策が機能したのかを数値化します。また、施策によって売上やコストがどのように変わったのかの確認も必要です。
施策の効果があった場合は、さらに効果的な施策を実施し、失敗した場合は失敗の原因を特定して再び改善策の実施と効果検証を行います。
QCDを生産管理に取り入れる手順
QCDを生産管理に取り入れる際は、「現場分析と改善目標の設定」「各要素ごとの改善計画の策定」「継続的なモニタリングと評価」の順で行います。
業種に関わらず、まずは現場がどのような状況で、どのような課題を抱えているのか把握しなければなりません。生産プロセスに問題はないのか、生産工程が他の工程とどのように関連しているのかを確認するのが重要です。
また、数値だけでなく現場で業務を行う従業員の意見も取り入れることで、より課題を明確化できます。課題を明確にすることで改善目標を設定も可能になります。
課題の明確化と改善目標の設定後にやるべきことは各要素ごとの改善計画の策定です。課題と改善目標を達成するために、どのような方法を取ればよいのかを決定し、実行に移します。
改善計画を実行したら実行成果を評価し、継続的にモニタリングします。成功、失敗の要因を分析し、QCDを改善し続けることが重要です。
生産性向上への道:QCD改善の重要性
生産管理においてQCDを改善することは企業の利益や顧客満足度の向上のために重要な要素です。QCDはそれぞれ3すくみの関係にあるため、バランスを見極めながら利益を最大化させる必要があります。
QCDを導入することで、ブランディングの強化や利益率の向上、納期遵守による顧客からの信頼といったメリットがあります。改善するためには課題の明確にし、改善策を行い、効果検証するといった手順を踏むのが重要です。
明確にした課題を改善するために効果的な方法のひとつが生産管理システムです。生産管理システムを導入する際は各システムを比較し、気になるシステムの資料をダウンロードして自社に合うのか検討してみましょう。
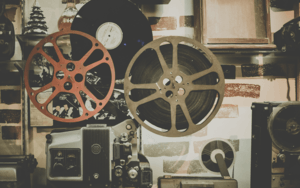
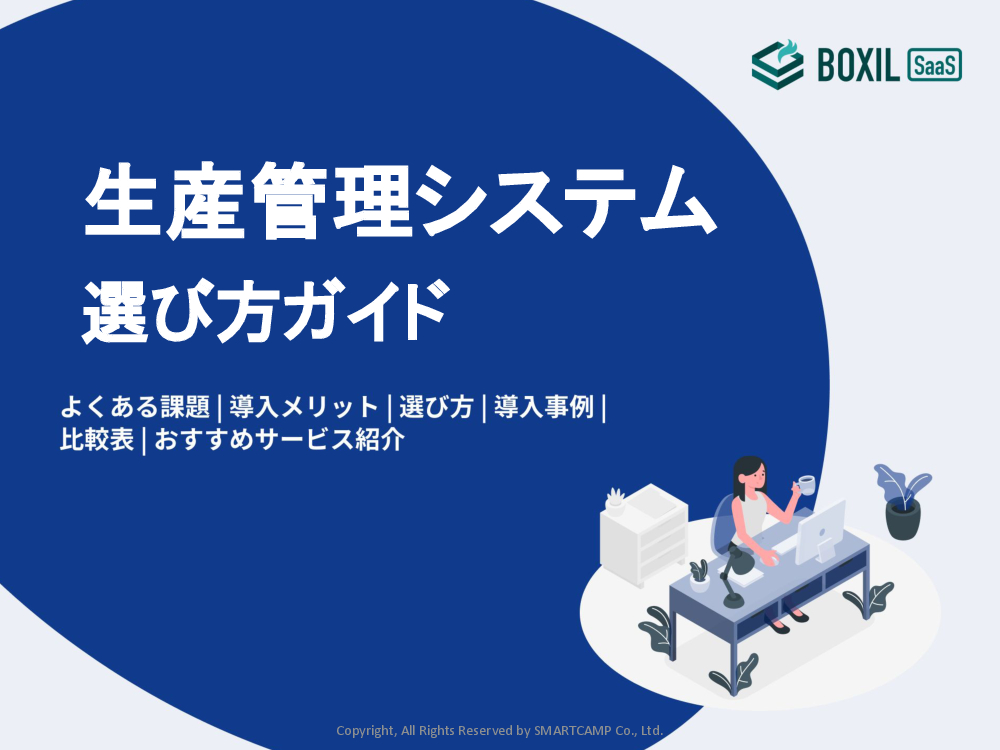