生産管理システムのメリット・デメリット!解決できる課題とポイント
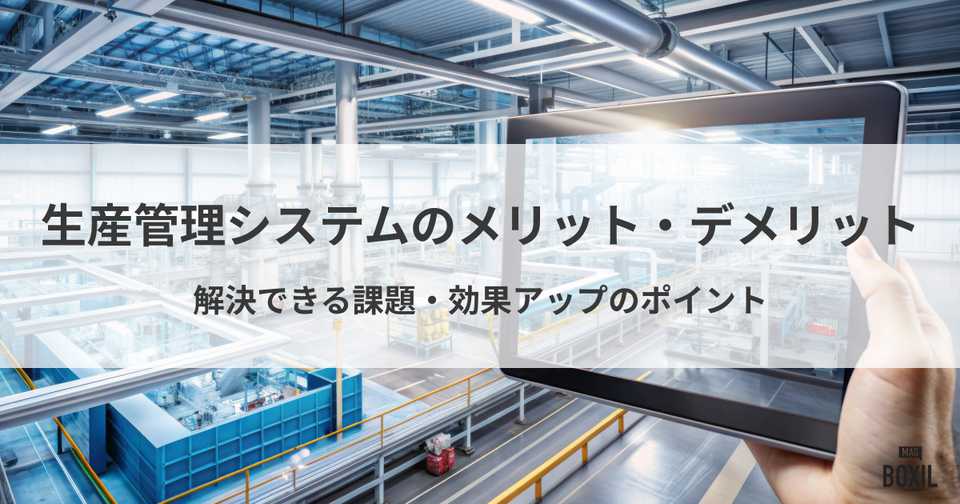
目次を閉じる
生産管理システムとは
生産管理システムとは、製造業における生産活動を効率的に管理するためのシステムです。製品の設計から製造、在庫管理、出荷まで、生産に関わるあらゆる情報を一元管理し、計画の立案や進捗管理、原価管理などを支援します。これにより、企業は生産性を向上させ、コストを削減し、顧客満足度を高められます。
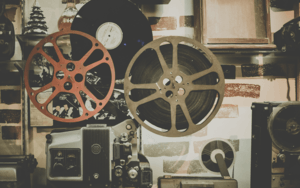
生産管理システムで解決できる課題
生産管理システムの導入により、製造業が直面する様々な課題を効果的に解決できます。以下に、代表的な5つの課題とその解決策を紹介します。
納期の遅延
納期の遅延は、顧客の信頼低下や違約金発生など、企業に大きな損失をもたらします。原因は生産計画の甘さや予期せぬトラブル、情報共有不足など多岐にわたります。生産管理システムを導入することで、正確な生産計画の立案や進捗状況のリアルタイム把握が可能になります。
また、部門間の円滑な情報共有により、納期遅延のリスクを大幅に軽減できます。結果として、顧客満足度の向上や企業評判の維持、不要なコスト発生の防止につながります。
原価管理の複雑さ
製造原価の正確な把握は収益性維持に不可欠ですが、材料費、労務費、経費など多様な要素から構成されるため、手作業での管理は煩雑です。適切な原価管理が行われないと、誤った価格設定や不要なコスト発生、経営判断の遅れにつながる恐れがあります。
生産管理システムを活用することで、各種原価の自動計算や正確な原価情報の取得が可能になります。さらに、過去データとの比較分析により、効果的なコスト削減ポイントの特定も容易になります。
在庫過多
在庫過多は、保管コストの増加、在庫の陳腐化、資金繰りの悪化など、様々な問題を引き起こします。需要予測の誤りや過剰生産、発注ミスなどが主な原因です。生産管理システムは、需要予測に基づいた適切な在庫管理を支援し、販売・生産状況のリアルタイム把握を可能にします。
これにより、適切な発注量の算出や在庫過多の防止が実現し、保管コストの削減や資金効率の改善、品質維持にも貢献します。
情報共有の不足
製造現場では多くの部門が関わるため、情報共有の不足はミスや手戻りの原因となり、業務効率を低下させます。また、部門間連携の困難さ、意思決定の遅れ、コミュニケーションエラーなどの問題も生じます。生産管理システムの導入により、各部門が同じ情報を共有できるプラットフォームが提供されます。
これにより、情報伝達のロスタイムが削減され、リアルタイムでの情報更新と共有が可能になります。結果として、部門間の連携強化や迅速な意思決定、品質向上につながります。
人材不足
近年、多くの製造業で人材不足が深刻化しており、生産性や品質の低下、従業員の負担増加などの問題が生じています。生産管理システムの導入により、業務の標準化や自動化が促進され、人材不足の解消に貢献します。
システムが業務をサポートすることで、従業員一人ひとりの負担が軽減され、生産性向上につながります。また、データに基づいた効率的な人員配置や、若手従業員の早期スキルアップも期待できます。
生産管理システムを導入するメリット
生産管理システムを導入することで、企業はさまざまなメリットを享受できます。生産管理システム導入の主なメリットは次の7つが挙げられます。
- 生産状況の可視化
- 在庫状況の可視化
- 業務効率化
- リードタイムの短縮
- コスト削減
- 属人化の防止
生産状況の可視化
生産管理システムを導入すると、生産の進捗状況をリアルタイムで把握できます。システム上で各工程の進捗状況や、作業者の稼働状況、設備の稼働状況などを可視化することで、生産全体の状況を容易に把握できます。
従来は、担当者が個別に進捗状況を管理していたため、全体像を把握するのに時間がかかっていました。しかし、生産管理システム導入後は、ダッシュボードで必要な情報を一目で確認できるようになり、迅速な状況把握が可能です。
この結果、生産状況の遅延や問題発生にいち早く気づき、対応できるようになります。また、正確な情報に基づいた生産計画の立案や調整が可能になり、生産性の向上につながります。
在庫状況の可視化
生産管理システムは、リアルタイムな在庫状況の把握を可能にします。システム上で原材料や仕掛品、完成品の在庫数量、保管場所、入出庫履歴などを一元管理することで、在庫状況を正確に把握できます。
従来はExcelを使って在庫管理を行っている企業も多く、情報が最新でないケースや、担当者によって情報に差異があるケースも見られました。しかし、生産管理システム導入後は、常に最新の在庫情報を確認できるようになり、在庫管理の精度が向上します。
これにより、在庫不足による機会損失や過剰な在庫による保管コストの増加を防げます。適切な在庫管理は、資金繰りの改善にもつながるでしょう。
業務効率化
生産管理システムは、さまざまな業務の自動化や効率化を実現します。たとえば、受発注管理、生産計画の立案、進捗管理、在庫管理、原価管理など、従来は手作業で行っていた業務をシステム化することで、大幅な時間短縮が可能です。
これまで、多くの担当者がルーチンワークに多くの時間を費やしていました。しかし、生産管理システム導入後は、システムがルーチンワークを自動的に処理してくれるため、担当者はより重要な業務に集中できるようになります。
その結果、従業員の負担軽減につながり、モチベーション向上や人材の定着につながるでしょう。また、業務効率化による残業時間の削減効果も見込めます。
リードタイムの短縮
リードタイムとは、顧客からの注文を受けてから製品を納品するまでの時間のことです。生産管理システムを導入することで、生産計画の精度向上や在庫管理の効率化、情報共有の促進などが実現し、リードタイムの短縮につながります。
従来は、各工程の進捗状況や在庫状況の把握に時間がかかっており、リードタイムが長くなってしまうケースがありました。しかし、生産管理システム導入後は、情報共有がスムーズになり、各工程が効率的に連携できるようになるため、リードタイムを短縮できます。
リードタイムの短縮は、顧客満足度向上に大きく貢献します。短納期対応が可能になることは、競争力の強化にもつながるでしょう。
コスト削減
生産管理システム導入により、さまざまなコスト削減効果が見込めます。具体的には、在庫管理の効率化による保管コストの削減、業務効率化による人件費の削減、生産性向上による製造コストの削減などです。
従来は、過剰な在庫を抱えていたり、非効率な作業によって人件費がかさんでいたりするケースも少なくありませんでした。しかし、生産管理システム導入後は、無駄なコストを削減し、経営の効率化が可能です。
コスト削減は、企業の収益力向上に直結します。また、削減できたコストを新たな投資や事業展開に活用することで、さらなる成長を促進できる可能性も秘めています。
属人化の防止
生産管理システムは、業務の標準化や情報の一元管理を促進することで、業務の属人化を防止します。
従来は、特定の担当者に業務が集中し、担当者不在の際に業務が滞ってしまうケースや、業務の引継ぎに時間がかかってしまうケースがありました。しかし、生産管理システム導入後は、誰でも同じように業務を遂行できるようになり、属人化によるリスクを軽減できます。
担当者の経験や勘に頼らない、標準化された業務プロセスを構築することは、品質の安定化にもつながります。
DXの推進
DX(デジタルトランスフォーメーション)とは、デジタル技術を活用して、企業のビジネスモデルや業務プロセスを変革することです。生産管理システムは、生産現場のデータ活用を促進し、DX推進の基盤となります。
従来は紙やExcelで管理していたデータを、システム上で一元管理することで、データの活用や分析が容易になるでしょう。蓄積されたデータを活用することで、需要予測や生産計画の精度向上、品質改善などにつなげられます。
DXを推進することで、企業は競争力を強化し、持続的な成長を遂げられるでしょう。
生産管理システムを導入するデメリット
生産管理システムの導入は多くのメリットをもたらしますが、同時にいくつかのデメリットも存在します。導入前に把握しておくべき代表的なデメリットを2つ紹介します。
導入・運用コストがかかる
生産管理システムを導入するには、初期費用とランニングコストがかかります。初期費用に含まれるのは、ソフトウェアの購入費や導入に伴うコンサルティング費用、カスタマイズ費用などです。
ランニングコストには、システムの保守費用やバージョンアップ費用、サポート費用などが含まれます。
導入するシステムや規模によっては、多額の費用が発生するでしょう。そのため、導入前に予算計画をしっかりと立てる必要があります。また、費用対効果をシミュレーションし、投資に見合う効果が得られるかどうかの検討も必要です。
従業員の理解が必要
生産管理システムを導入しても、従業員がシステムの利用方法を理解していなければ、効果的に活用できません。特に、従来の業務プロセスから大きく変わる場合は、従業員の抵抗感や、システムへの理解不足が生じるかもしれません。
導入前に、従業員に対してシステムの目的やメリット、使用方法などを説明しましょう。また、操作研修を実施し、システムを使いこなせるようにサポートすることも重要です。システム導入後も、継続的なサポート体制を構築することで、従業員の不安や疑問を解消する必要があります。
生産管理システムの導入効果を高めるポイント
生産管理システムを導入するだけでは、期待する効果を得られないでしょう。導入効果を最大化するためには、いくつかのポイントを押さえる必要があります。生産管理システム導入を成功させるためのポイントを5つ紹介します。
解決したい課題を明確にする
生産管理システムを導入する目的を明確化し、解決したい課題を具体的に洗い出しましょう。納期遅延を解消したい、在庫管理を効率化したい、原価管理を正確に行いたいなど、自社の課題を明確にすることで、最適なシステム選びや、効果的な運用につなげられます。
課題が明確になると、システムに求める機能や要件を具体的に決められます。たとえば、納期遅延を解消したい場合は、工程管理機能や進捗管理機能の充実したシステムが適しているでしょう。このように、課題解決に焦点を当てることで、導入効果を高められます。
段階的に導入する
生産管理システムを一度に全社導入しようとすると、従業員の負担が大きくなり、混乱を招くかもしれません。そのため、まずは一部の部門や工程から導入し、段階的に範囲を広げていく方法が有効です。
たとえば、在庫管理に課題を感じている場合は、まず倉庫部門にシステムを導入し、在庫管理業務を効率化します。その後、効果を検証しながら、他の部門や工程にもシステムを導入することで、スムーズな移行が可能になります。
トップダウンで導入・運用を進める
生産管理システムの導入や運用には、経営層の理解と協力が不可欠です。経営層が率先して導入を推進することで、従業員の意識改革や、スムーズな運用体制の構築につながります。
経営層がシステム導入の意義や目的を明確に示し、全社的な取り組みとして推進することで、従業員のモチベーション向上や協力体制の構築を促せます。また、経営層が積極的にシステムを活用することで、従業員の模範となり、システムの定着を促進できるでしょう。
運用体制とマニュアルの構築
生産管理システムを効果的に運用するためには、運用体制を構築しましょう。システムの管理責任者を決め、各部門の担当者との連携をスムーズに行える体制を整えなければなりません。
また、システムの操作方法やトラブルシューティングなどをまとめたマニュアルを作成することで、従業員がシステムをスムーズに利用できる環境を整えられます。マニュアルはわかりやすく、最新の情報に更新されている状態を保ちましょう。
定期的に効果検証する
生産管理システム導入後は、定期的に効果検証を行い、改善をくり返していきましょう。システム導入によって、当初の目的が達成されているか、業務効率が向上しているか、コスト削減効果が出ているかなどを検証します。
効果検証の結果を踏まえ、システムの設定変更や運用方法の見直し、従業員への追加研修など、改善策を検討しましょう。PDCAサイクルを回すことで、システムを継続的に改善し、導入効果を最大化できます。
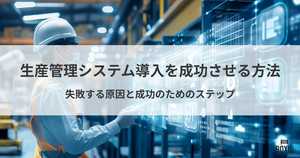
効果的な運用で生産管理システムのメリットを最大化しよう
生産管理システムを導入することで、生産状況の可視化、在庫状況の可視化、業務効率化、リードタイムの短縮、コスト削減、属人化の防止、DXの推進など、さまざまなメリットを得られます。
生産管理システムのメリットを最大限に引き出すためには、解決したい課題を明確にし、段階的に導入を進めることが重要です。トップダウンで運用を進めること、運用体制とマニュアルを構築すること、定期的に効果検証を行うことなどのポイントも押さえておきましょう。
システムを効果的に運用することで、企業は生産性を向上させ、コストを削減し、競争力を強化できるでしょう。
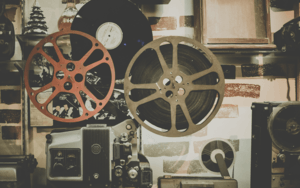
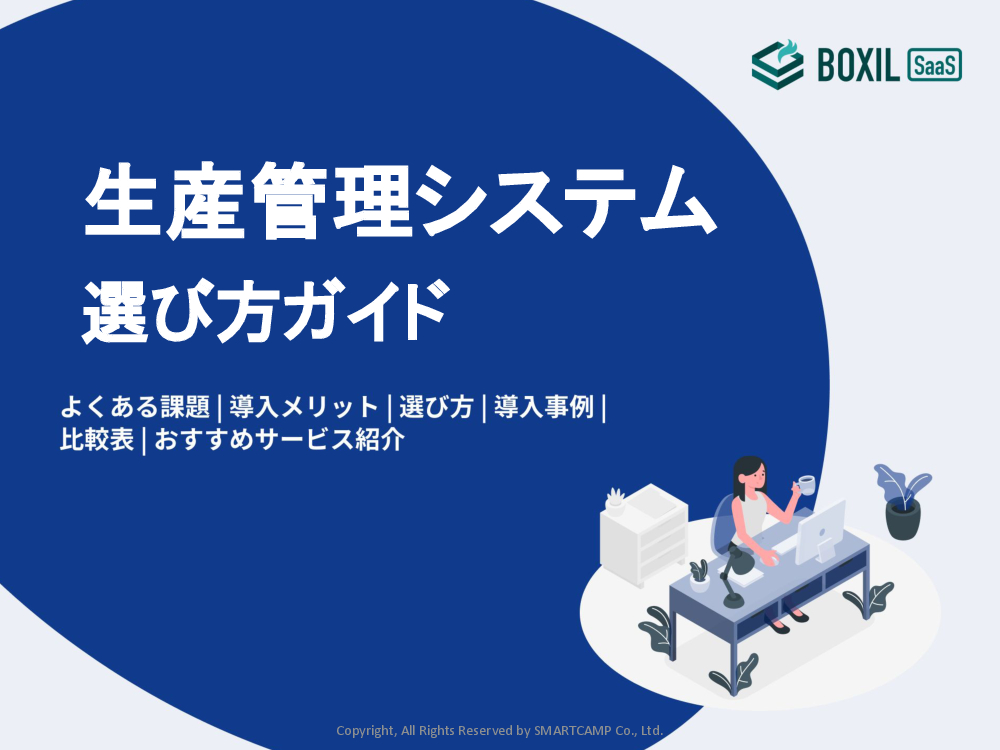