生産拠点を最適化するには?検討すべきポイントと手順
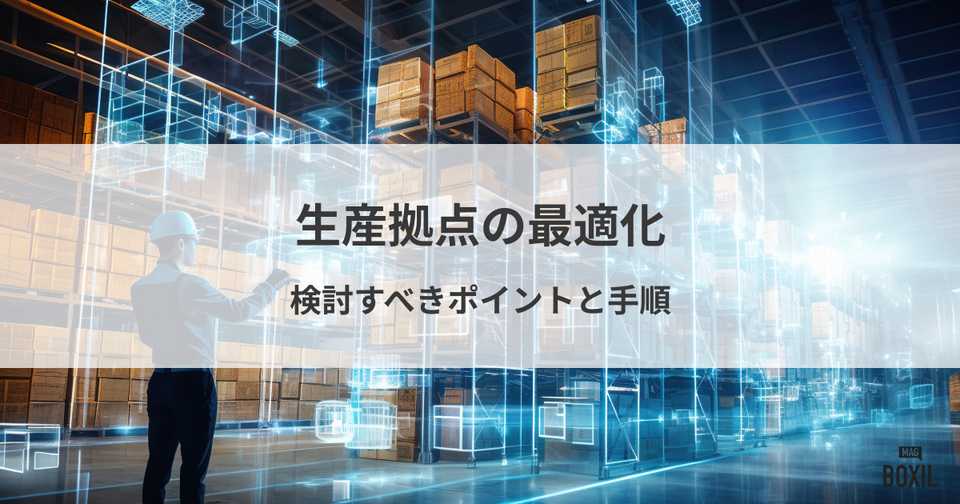
目次を閉じる
生産拠点とは
生産拠点とは、製品を製造するための設備や人員が集約された場所です。具体的には工場や製造施設などを指します。
たとえば自動車メーカーであれば、自動車を組み立てる工場が生産拠点です。食品メーカーなら、食品を加工・製造する工場が生産拠点となります。このように業種や製品によって、さまざまな形態の生産拠点が存在しています。
企業は社会において、製品を効率的に生産し、市場に供給する重要な役割を担います。生産拠点は企業の競争力に大きく影響を与える要素のひとつです。そのため、生産拠点の立地や運営方法は経営戦略上、重要な意味を持ちます。
生産拠点の最適化とは
生産拠点の最適化とは、企業の生産活動における拠点配置や運営方法を見直し、最適な状態にすることです。
具体的には、生産コストの削減、リードタイムの短縮、品質の向上などを目指し、立地、生産能力、物流、人材配置などを総合的に検討します。これにより、企業は変化する市場環境に柔軟に対応し、競争優位性を確立できます。
生産拠点の最適化を図る必要性
グローバル化が進み、市場環境が急速に変化する現代において、生産拠点の最適化は企業にとって不可欠な取り組みとなりました。新興国の台頭や地政学リスクの高まり、自然災害の頻発など、企業を取り巻く環境は常に変化しています。
このような状況下で、従来の生産体制を維持していては、競争力を維持することは困難です。企業は常に変化に対応し、最適な生産体制を構築していく必要があり、そのための重要な手段が生産拠点の最適化です。
生産拠点の最適化で期待できる効果
生産拠点の最適化によって得られる効果は次のとおりです。
- 物流コストの削減による利益率の向上
- 生産効率の改善による生産能力の増強
- リスク分散によるサプライチェーンの安定化
これらの効果は企業の収益性向上に直結するだけでなく、顧客への安定供給や品質向上にもつながり、顧客満足度の向上にも貢献します。また、環境負荷の低減や地域社会への貢献など、企業としての社会的責任を果たすうえでも重要です。
生産拠点を最適化するために考えること
生産拠点を最適化するうえで、まずは分散生産か集中生産か、国内生産か海外生産かを考える必要があります。
分散生産と集中生産
生産拠点を分散させるか、一箇所に集中させるかという観点について説明します。それぞれにメリットとデメリットが存在し、企業の戦略や製品特性によって最適な選択肢は異なります。
分散生産が適したケース
分散生産は、複数の拠点に生産機能を分散させる方式です。
分散生産のメリットは、需要地に近い場所で生産することで輸送コストを削減できる点や、災害時のリスク分散効果が期待できる点です。デメリットとしては、各拠点での設備投資や管理コストの発生による全体としてのコスト増加、品質管理の難しさが挙げられます。
分散生産が適しているのは、地域ごとのニーズに合わせた製品を生産する場合や、輸送コストが高い製品を扱う場合、地産地消を重視する場合などです。また、大規模災害のようなリスクに備えて生産拠点を分散させたい場合にも適しています。
たとえば、地域ごとに味の好みが異なる食品や、輸送に大きなコストがかかる飲料水などが該当します。
集中生産が適したケース
集中生産は、限られた拠点に生産機能を集中させる方式です。
集中生産のメリットとして、規模の経済性を活かして生産コストを削減できる点や、高度な技術や設備を集約することで高品質な製品を効率的に生産できる点が挙げられます。
デメリットは、需要地までの輸送コストが増加しやすいこと、災害時に生産が完全に停止してしまうリスクがあることなどです。
集中生産が適しているのは、高度な技術や設備が必要な製品を生産する場合や、グローバル市場で均一な品質の製品を供給する場合などです。また、生産量が非常に多く、規模の経済性を追求する場合にも適しています。
たとえば、高度な技術を要する半導体や、世界中で同じ品質が求められる高級ブランド品などが該当します。
国内生産と海外生産
分散生産・集中生産と同様に、それぞれにメリットとデメリットが存在し、企業の戦略や製品特性によって最適な選択肢は異なります。
国内生産が適したケース
国内生産は、生産拠点を国内に置く方式です。
国内生産のメリットは、言語や文化の障壁が少なく、コミュニケーションが円滑に進めやすい点や、品質管理が行き届きやすい点、知的財産権の保護が比較的容易な点などです。デメリットとしては、人件費や地価などのコストが高くなりやすいこと、海外市場への進出が遅れやすいことなどが挙げられます。
国内生産が適しているのは、高い品質管理が求められる製品を生産する場合や、顧客との密な連携が必要な場合、国内市場を主要なターゲットとしている場合などです。また、技術流出のリスクを避けたい場合にも適しています。
たとえば、高い精度が求められる精密機器や、顧客の要望に合わせたカスタマイズが必要な製品などが該当します。
海外生産が適したケース
海外生産は、生産拠点を海外に置く方式です。
海外生産のメリットは、人件費や地価などのコストを削減しやすいことや、海外市場へのアクセスが容易になること、現地の優遇税制を活用できることなどです。デメリットとしては、言語や文化の障壁、品質管理の難しさ、政治情勢やカントリーリスクの影響などが挙げられます。
海外生産が適しているのは、コスト競争力が重要な製品を生産する場合や、海外市場を主要なターゲットとしている場合、現地の資源や労働力を活用したい場合などです。たとえば、大量生産されるアパレル製品や、資源が豊富な地域で生産する鉱産物などが該当します。
生産拠点の最適化で検討すべき4つのポイント
生産拠点の最適化を進めるうえで特に重要なポイントは次の4点です。これらの要素を十分に検討することで、より効果的な拠点戦略を立てられるようになります。
- 物流
- 法令や規制
- 土地固有のリスク
- 労働者の確保しやすさ
ポイント1. 物流
物流を検討する際には、輸送コスト、リードタイム、輸送手段の選択肢、倉庫の確保などを調査・検討します。特に、原材料の調達から製品の出荷まで、サプライチェーン全体を通して物流コストと時間を最小限に抑えることを意識しなければなりません。
また、輸送ルートの天候リスクや地政学リスクなども考慮に入れる必要があります。
これらのポイントを検討することで、物流コストの削減、リードタイムの短縮、サプライチェーンの安定化などが可能です。これにより、製品の競争力強化、顧客への迅速な納品、安定的な生産体制の構築につながります。
ポイント2. 法令や規制
法令や規制を検討する際には、環境規制、労働法、税制、輸出入規制、知的財産権保護などを調査・検討します。特に、操業許可の取得や環境基準への適合など、事業運営に直接影響する法令や規制を事前に把握し、遵守することを意識しなければなりません。
また、将来的な法改正のリスクも考慮に入れる必要があります。
これらのポイントを検討することで、法令違反による操業停止リスクの回避、税制優遇措置の活用、事業運営の円滑化などが可能です。これにより、安定的な事業運営、コスト削減、競争力強化につながります。
ポイント3. 土地固有のリスク
土地固有のリスクを検討する際には、自然災害リスク(地震、津波、洪水など)、地盤の安定性、インフラの整備状況、治安状況などを調査・検討します。特に、事業継続に大きな影響を与える可能性のある自然災害リスクを十分に評価し、適切な対策を講じることを意識しなければなりません。
これらのポイントを検討することで、自然災害などによる事業中断リスクの軽減、従業員の安全確保、事業継続計画の策定などが期待できます。これにより、事業の安定性向上、リスクマネジメントの強化につながります。
ポイント4. 労働者の確保しやすさ
労働者の確保しやすさを検討する際には、労働市場の状況(労働力人口、失業率など)、賃金水準、労働者のスキル、教育機関の状況などを調査・検討します。特に、必要なスキルを持つ労働者を安定的に確保できるかどうかを意識しなければなりません。
また、労働者の定着率を高めるための福利厚生や労働環境なども考慮に入れる必要があります。
これらのポイントを検討することで、必要な人材の確保、労働コストの最適化、従業員のモチベーション向上などが可能です。これにより、生産性の向上、品質の安定、企業競争力の強化につながります。
生産拠点の最適化プロジェクトの手順
ここでは、生産拠点の最適化プロジェクトを進めるための具体的な手順について解説します。これらの手順に沿って進めることで、プロジェクトを円滑に進め、所期の目的を達成できるでしょう。
- プロジェクトチームの立ち上げ
- 現状の課題の洗い出し
- 目標設定
- 候補地の選定
- 費用対効果の検証
- 各種業者の選定
手順1. プロジェクトチームの立ち上げ
プロジェクトチームの立ち上げでは、プロジェクトの責任者を選定し、関連部署からメンバーを集めてチームを編成します。チームメンバーには、生産、物流、財務、法務など、関連する専門知識を持つ人材を含めましょう。
また、プロジェクトの目的、スコープ、タイムラインなどを明確に定義し、関係者間で共有します。
適切なチームを立ち上げることで、各部門の専門知識を集結させ、多角的な視点から検討を進められます。また、責任者と役割分担を明確にすることで、プロジェクトの進行を円滑にし、意思決定の迅速化を図れます。
手順2. 現状の課題の洗い出し
現状の課題の洗い出しでは、現在の生産拠点における問題点や改善点を洗い出します。具体的には、生産効率、物流コスト、品質、リードタイム、リスクなどを分析し、ボトルネックとなっている箇所や改善が必要な箇所を特定します。
現場の担当者へのヒアリングやデータ分析などを通して、客観的な課題を抽出しましょう。
課題を明確にすることで、最適化プロジェクトの具体的な目標設定が可能になり、効果的な改善策を検討できます。また、課題を定量的に把握することで、改善効果を測定するための基準にできます。
手順3. 目標設定
目標設定では、洗い出した課題を踏まえ、最適化プロジェクトで達成すべき具体的な目標を設定します。目標は、たとえば生産コストを〇%削減、リードタイムを〇日短縮、品質不良率を〇%改善といった形で、定量的かつ明確に設定します。
また、目標達成のためのKPIを設定し、進捗状況をモニタリングできるようにしましょう。
明確な目標を設定することで、プロジェクトの方向性が定まり、関係者間の認識を一致させられます。また、KPIを設定することで、進捗状況を客観的に評価し、必要に応じて軌道修正を行えます。
手順4. 候補地の選定
候補地の選定では、目標に基づき、立地条件、物流、法令・規制、土地固有のリスク、労働力などを考慮して、複数の候補地を選定します。各候補地について詳細な調査を行い、メリットとデメリットを比較検討します。必要に応じて、現地視察も行いましょう。
適切な候補地を選定することで、将来的な事業運営におけるリスクを最小限に抑え、最適な事業環境を確保できます。また、複数の候補地を比較検討することで、より客観的な判断が可能になります。
手順5. 費用対効果の検証
費用対効果の検証では、各候補地における建設コスト、運営コスト、物流コスト、税制優遇措置などを詳細に試算し、投資回収期間やROIなどを評価します。定量的データに基づいて費用対効果を比較検討し、最適な候補地を選定しましょう。
費用対効果を検証することで、投資に見合う効果が得られるかどうかを客観的に判断できます。これにより、無駄な投資を避け、効率的な資源配分を行えます。
手順6. 各種業者の選定
建設業者や不動産業者などの各種業者の選定では、複数の業者から見積もりを取り、実績、技術力、価格などを比較検討します。業者との契約条件を明確にし、プロジェクトの円滑な進行を確保しましょう。
適切な業者を選定することで、高品質な設備導入や効率的な物流体制の構築が可能になります。また、業者との良好な関係を構築することで、長期的な事業運営を円滑に進められるでしょう。
生産拠点の最適化でコスト削減と収益アップを
グローバル化が進み市場環境が激しく変化する現代において、生産拠点の最適化は、企業が持続的な成長を遂げるために不可欠な取り組みです。変化への対応、競争力の維持・強化という観点から、生産拠点を最適化する重要性は高まり続けています。
生産拠点の最適化は、単なるコスト削減に留まりません。最適な拠点配置と運営は、物流コストや生産コストの削減、リードタイムの短縮、品質向上などをもたらし、結果として企業の利益率向上につながります。
変化に柔軟に対応し、効率的な生産体制を構築することで、企業は競争優位性を確立し、収益アップを実現できるでしょう。