生産ロスとは?16の種類とロスを減らす方法を解説
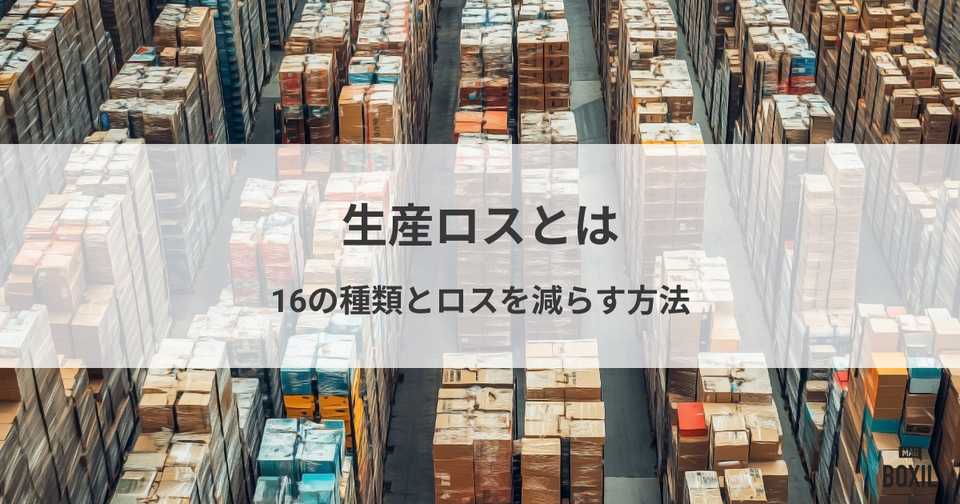
目次を閉じる
生産ロスとは
生産ロスとは、製造現場で発生するさまざまな損失のことです。これは、製品の製造過程で発生するムダであり、材料費や時間、人材、エネルギーなど、あらゆる資源の浪費につながります。
生産ロスは大きく分けて、設備のロス、人のロス、原単位のロスの3つに分類できます。これらのロスを削減することは、企業の収益性向上に不可欠です。生産ロスを放置すると、無駄なコストが増加し、競争力が低下してしまうでしょう。そのため、企業は生産ロスを最小限に抑えるための努力を続ける必要があります。
設備のロス
設備のロスは、機械や設備が本来の能力を発揮できないことで発生する損失です。設備のロスにはさまざまな種類があり、それぞれ原因と影響が異なります。
故障ロス
故障ロスとは、設備が突発的な故障によって停止することで発生する損失です。これにより、生産ラインの停止や納期遅延といった問題が生じます。故障ロスは、設備の老朽化やメンテナンス不足などが原因です。
故障ロスは、設備の経年劣化やメンテナンス不足、操作ミスなどによって引き起こされます。定期的なメンテナンスや点検を実施し、故障を未然に防がなければなりません。また、作業員への適切な教育訓練も故障ロス削減につながります。
段取り・調整ロス
段取り・調整ロスとは、製品の切り替え時に発生する準備作業による損失です。これは、機械の停止時間や調整作業時間などを含みます。
段取り・調整ロスは、作業手順の非効率性や作業者のスキル不足などが原因です。段取り作業の標準化や作業者のスキル向上を図ることで、ロスを削減できます。
刃具交換ロス
刃具交換ロスとは、切削工具のような刃物を交換するために生産を中断することで発生する損失です。これは、工具の寿命や摩耗によって交換が必要になる場合に発生します。
刃具交換ロスは、刃具の材質や加工条件、切削油の管理などが原因です。適切な刃具の選定や加工条件の見直し、切削油の適切な管理を行うことで、ロスを削減できます。
立上がりロス
立上がりロスとは、生産開始直後や設備の停止後、再び稼働させる際に発生する損失です。これは、機械の暖機運転や調整作業など、安定稼働までに時間を要するために発生します。
立上がりロスは、設備の特性や運転方法、作業者のスキルなどが原因です。設備の保温対策や運転方法の見直し、作業者のスキル向上を図ることで、ロスを削減できます。
チョコ停・空転ロス
チョコ停・空転ロスとは、機械の些細なトラブルや一時的な停止によって発生する損失です。これは、異物の混入やセンサーの誤作動など、予期せぬ原因で発生することが多いです。
チョコ停・空転ロスは、設備のメンテナンス不足や作業環境の悪さ、作業者の不注意などが原因となります。定期的な清掃や点検、作業環境の改善、作業者への教育訓練を行うことで、ロスを削減できます。
速度低下ロス
速度低下ロスとは、設備が設計上の速度で稼働できないことによって発生する損失です。これは、設備の老朽化やメンテナンス不足、材料の供給不足などが原因です。定期的なメンテナンスや点検を実施し、設備の性能を維持しましょう。
不良・手直しロス
不良・手直しロスとは、不良品の発生や手直し作業によって発生する損失です。これは、材料の不良や機械の不具合、作業ミスなどが原因です。材料の受入検査の強化や機械のメンテナンス、作業者への教育訓練を行うことで、ロスを削減できます。
シャットダウンロス
シャットダウンロスとは、設備のメンテナンスや清掃、点検などのために生産を停止することで発生する損失です。これは、定期的なメンテナンスや法令で定められた点検などで発生します。
シャットダウンロスは、設備のメンテナンス計画や作業手順などが原因です。メンテナンス計画の見直しや作業手順の効率化を図ることで、ロスを削減できます。
人のロス
人のロスは、作業者の行動や管理体制に起因する損失です。設備のロスとは異なり、人のロスは作業者の動きや判断、組織運営によって発生します。
管理ロス
管理ロスとは、管理業務の不備や非効率性によって生じる損失です。管理ロスは、現場作業の遅延や混乱を招きます。
管理ロスは、情報共有不足や意思決定の遅さ、適切な管理体制の欠如などが原因です。情報共有の仕組みを整備したり、意思決定プロセスを迅速化したりすることで、ロスを削減できます。
動作ロス
動作ロスとは、作業者の無駄な動作によって生じる損失です。動作ロスは、作業時間の浪費や作業者の疲労蓄積につながります。
動作ロスは、作業手順の不明確さや作業環境の不備、作業者のスキル不足などが原因です。作業手順を最適化したり、作業環境を改善したり、作業者の教育訓練を実施したりすることで、ロスを削減できます。
編成ロス
編成ロスとは、人員配置の不適切さによって生じる損失です。編成ロスは、作業効率の低下や納期遅延につながります。
編成ロスは、作業内容に対する人員配置のミスマッチやコミュニケーション不足、人員計画の不備などが原因です。作業内容に合わせた適切な人員配置を行ったり、作業者間の連携を強化したりすることで、ロスを削減できます。
自動化置換ロス
自動化置換ロスとは、本来自動化できる作業を手作業で行っていることによって生じる損失です。自動化置換ロスは、生産性の低下や人件費の増加につながります。
自動化置換ロスは、自動化技術に対する知識不足や導入コストへの懸念、人員配置の変更への抵抗などが原因です。自動化技術の導入を検討したり、導入後の人員配置計画を策定したりすることで、ロスを削減できます。
測定調整ロス
測定調整ロスとは、測定作業や調整作業に必要以上に時間を要することで生じる損失です。測定調整ロスは、生産時間の浪費につながります。
測定調整ロスは、測定機器の選定ミスやメンテナンス不足、調整作業の手順化不足などが原因です。適切な測定機器を選定したり、定期的なメンテナンスを実施したり、調整作業の手順を明確化したりすることで、ロスを削減できます。
原単位のロス
原単位のロスとは、製品を生産するために投入した資源(原材料、エネルギーなど)に対して、実際に得られた製品の量との差によって生じる損失です。
歩留まりロス
歩留まりロスとは、原材料から最終製品を生産する過程で発生する損失です。具体的には、加工中に発生する端材や不良品などによって失われる原材料が該当します。歩留まりロスが大きいと、原材料費が無駄になり、製品の原価が上昇します。
歩留まりロスは、原材料の品質不良、加工条件の不適切さ、作業者の技術不足、設備の老朽化などが原因です。原材料の品質管理を徹底したり、加工条件を最適化したり、作業者の教育訓練を実施することで、ロスを削減できます。
エネルギーロス
エネルギーロスとは、生産活動に使用したエネルギーが有効に活用されずに失われる損失です。具体的には、機械の空運転時の電力消費、排熱として放出される熱エネルギー、照明や空調などの無駄な使用などが該当します。エネルギーロスが大きいと、光熱費が増加し、環境負荷も高まります。
エネルギーロスは、設備の断熱不足、運転方法の不適切さ、エネルギー管理の不備などが原因です。設備の断熱改修を行ったり、運転方法を見直したりすることで、ロスを削減できます。
型・治具ロス
型・治具ロスとは、製品の製造に使用する型や治具の劣化や破損によって生じる損失です。型・治具ロスが大きいと、製品の品質や生産効率の低下につながります。
型・治具ロスは、型や治具の材質選定ミス、使用方法の不適切さ、メンテナンス不足などが原因です。適切な材質の型や治具を選定したり、使用方法を徹底したり、定期的なメンテナンスを実施することで、ロスを削減できます。
生産ロスを削減する6つのポイント
生産ロスは、企業にとって収益低下の大きな要因となります。ロスを削減するためには、多角的な視点からの取り組みが不可欠です。生産ロスを削減するための重要な6つのポイントを紹介します。
ポイント1. 現状の把握と原因究明
生産ロス削減のために、まず現状を正しく把握し、ロスが発生している原因を特定しましょう。そのためには、過去のデータ分析や現場調査、作業者へのヒアリングなどを行い、定量的なデータと定性的な情報を集める必要があります。
現状把握と原因究明を徹底することで、ロスの発生箇所と原因が明確になり、効果的な対策の立案・実行が可能です。これにより、無駄な対策を防ぎ、効率的にロスを削減できます。
ポイント2. 業務の分析と問題点の改善
業務フローを可視化し、各工程における無駄やボトルネックを分析しましょう。そのうえで、作業手順の見直しやレイアウトの改善、使用する設備・工具の最適化などを検討し、問題点を改善していく必要があります。
業務の分析と問題点の改善に取り組むことで、作業効率が向上し、リードタイムの短縮や人的ミスの削減が可能です。また、作業者の負担軽減にもつながり、モチベーション向上も期待できます。
ポイント3. TPMの導入
TPM(Total Productive Maintenance:全員参加の生産保全)は、作業効率の最大化を目指す活動です。設備の自主保全や計画保全、品質保全などを通じて、故障ロスやチョコ停ロスといった設備のロスを削減します。
TPMを導入することで、設備の故障頻度を減らし、安定稼働時間を増やせます。また、作業者自身が設備の保全に関わることで、設備への意識が高まり、適切な操作やメンテナンスが行われるようになるでしょう。
ポイント4. 5S活動の導入
5S(整理・整頓・清掃・清潔・躾)は、職場環境を整備するための活動です。整理で不要なものを排除し、整頓で必要なものを使いやすい場所に配置し、清掃で職場を清潔に保ちます。清潔で整理整頓された状態を維持し、躾でルールを守る習慣を定着させます。
5S活動を導入することで、作業効率の向上や安全性の確保、品質の向上などが可能です。また、職場環境が改善されることで、作業者のモチベーション向上にもつながります。
ポイント5. コミュニケーションの活性化
作業者間や部署間のコミュニケーションを活性化することで、情報共有がスムーズになり、連携が強化されます。これにより、作業の連携ミスや情報伝達の遅延によるロスの削減が可能です。
コミュニケーションの活性化は、問題の早期発見や迅速な対応につながります。また、作業者間の相互理解が深まり、より良い改善提案が生まれる可能性もあります。
ポイント6. IT技術の活用
生産管理システムやIoTなどのIT技術を活用することで、生産状況の可視化やデータ分析が可能です。これにより、ロスの発生状況をリアルタイムに把握し、迅速な対応を取れます。
IT技術の活用により、データに基づいた客観的な分析が可能になり、より効果的なロス削減策を立案できるでしょう。作業の自動化や省人化にもつながり、生産性の向上に大きく貢献します。
生産ロスを削減し、コスト削減と収益性向上を
生産ロスは材料費やエネルギーだけでなく、時間や人材の浪費にもつながり、企業の収益性を損なう要因です。生産ロス削減は、企業の競争力と成長に不可欠といえます。
そして、これらのロス削減には生産管理システムの活用が有効です。生産状況の可視化やデータ分析、作業効率化などを支援し、遅延防止、改善策の立案、人的ミスの削減などに貢献します。ロス発生の未然防止や迅速な対応を可能にするため、生産ロス削減と収益性向上を目指すうえで、生産管理システムの導入と運用は強力な武器となるでしょう。
こちらの記事ではおすすめの生産管理システムを紹介しています。生産管理システムに興味がある方、生産ロスの削減を目指す方は、ぜひお読みください。
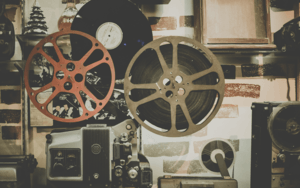